Equipoise
Design # 135; Equipoise
Built by: Brooklin Boatyard
Launch: May, 2021
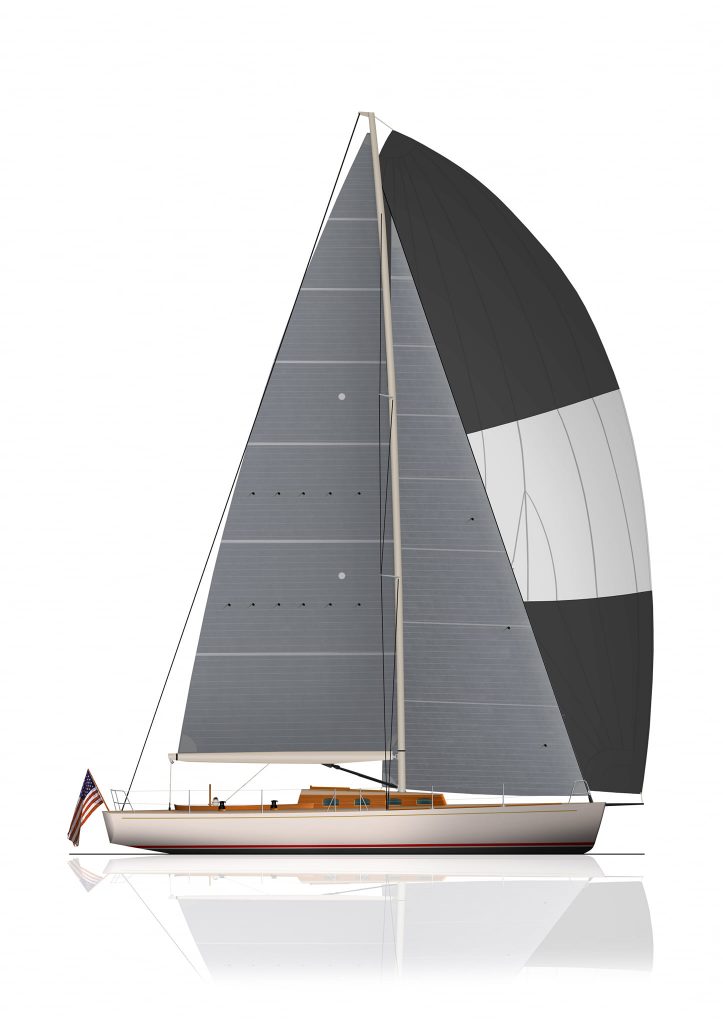
Rendering courtesy BBY
DESIGN #135: 44.4 ft LOA Racer/ Cruiser: 2/17/21
Specifications:
LOA | 44.4 ft |
LWL | 36.2 ft |
Max Beam | 12.0 ft |
Draft | 7.8 ft |
Disp (Meas Trim) | 13,500 lbs |
Ballast | 5,920 lbs |
Sail Area (RSAT) | 963 ft² |
IM | 55.5 ft |
J | 16.3 ft |
LP | 106% |
P | 55.4 ft |
E | 19.8 ft |
LOA 44.4 ft Sail Area (RSAT) 963 ft^2
LWL 36.2 ft ‘IM’ 55.5 ft
Max Beam 12.0 ft ‘J’ 16.3 ft
Draft 7.8 ft ‘LP’ 106%
Disp (Meas Trim) 13,500 lbs ‘P’ 55.4 ft
Ballast 5,920 lbs ‘E’ 19.8 ft
Equipment:
Spars: Offshore Spars; custom carbon mast & boom, w/2 swept spreaders & in-boom furling
Winches: Harken; 2×50.2STEP primaries, 2×46.2STEP mainsheet, 2×46.2STEP housetop Electronics: Owner option
Auxiliary: Electric Yacht ‘Quiet Torque 20.0 SD’ electric drive w/Victron LiFePO4 batteries
Builder:
Brooklin Boatyard, Brooklin, ME
Design Comments:
The commission for Equipose came from a repeat customer of both this office and of Brooklin Boatyard. During the summers on the east coast he sails Dreadnought, the first of our three T49c designs, out of Southwest Harbor, Maine. In the winter on the west coast, he has been sailing a BBW 47 out of Marina del Rey that he decided to replace with a boat that is a lot faster and less challenging to maintain (via less brightwork) in the hot SoCal sun.
Dreadnought (along with her near sisters Blackfish and Rascal) is long and lean and an upwind oriented boat. Equipoise is a foot longer on the water, a bit beamier (especially aft) and 3,500 pounds lighter, so she will be substantially faster cracked off, reaching, and running. The shape of her immersed volume forward is quite similar to that of Sforzando, an earlier 44 foot race boat that was a perennial winner in both IMS and IRC, but aft the new boat is considerably broader and more powerful. She will be club raced frequently, so the focus is on performance throughout, with hull, appendage, and rig detailing that is state of the art. However, she will also be daysailed routinely, and for ease of handling shorthanded, she features electrically driven main and headsail furling, as well as electric winches. Her styling is a lively mix of contemporary racer (with more stem rake forward and overhang aft) with a timeless Spirit of Tradition cabin house. We have been referring to her as a ‘performance day boat’.
The hull and deck are constructed with the cold molded wood/epoxy technique for which Brooklin Boatyard is justifiably famous. The hull features tongue and groove larch planking each side of diagonal paulonia veneers, while the deck is a sandwich of Okoume plywood over 5/8” thick CoreCell foam. The hull is overlaid with an e-glass finish layer. The stem, keelson, and ring frames are laminated Port Orford cedar. The keel loads are supported and distributed by a grid of laminated keel floors that are capped with unidirectional carbon fiber. Cold molded wood construction results in high strength and toughness relative to weight, and it is doubly attractive in that it also provides very impressive acoustic and thermal insulation. A noteworthy feature of Equipoise is her electric drive auxiliary, powered by lithium ion batteries that will be charged via solar cells and shore power. The interior is exquisitely detailed in a classic ‘Herreshoff’ style, with off-white painted surfaces trimmed with brightwork highlights that are a Brooklin Boatyard trademark.
The light weight construction of Equipose allows a high ballast/displacement ratio, that combined with a carbon rig, provides ample stability to support a generous sailplan. The large foretriangle is filled with a 106% overlap jib that is managed by an underdeck Selden electric furler . The main traveller is controlled by a Harken ‘Flatwinder 250’ line driver, and the hydraulic backstay pump is electrically driven as well. Downwind, asymmetricals and Code sails will be tacked to the end of a 3foot carbon fiber bowsprit.
Her unusual combination of eclectic style with contemporary performance will make her a stand out from the crowd, and ahead of the pack, in Southern California.
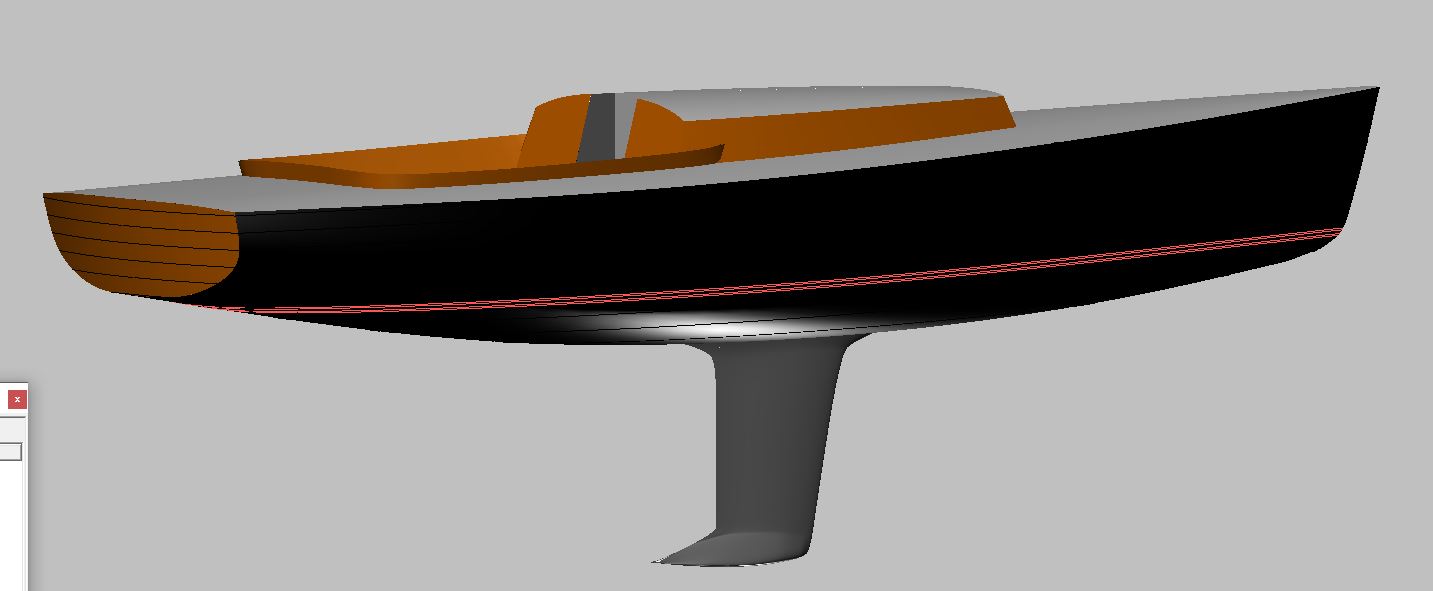

A 3-d surface model for the hull, deck, cabin house, cockpit and appendages is part of the design package, as well as 2-d drawings for the layout and structure. The Brooklin Boatyard design office then melds these together into one 3-d model that details virtually every component to be installed in the boat.
Each tongue and groove larch plank is bonded with epoxy resin to the next, as well as to the laminated keelson, the keel floors, many of the permanent internal panels, and some temporary forms where needed.
The off axis paulonia veneers are laid over, and bonded to, the tongue and groove inside skin. An outside skin of larch at 0-degree will follow.
The keel floors are capped with a thick layer of unidirectional carbon fiber.
Auxiliary power in a box! Two Electric Yacht motors are mounted to a Twin Disc strut drive, and are powered by lithium iron batteries that are charged via shore power and by solar panels located on the aft deck. Compared to a diesel, the equipment is more expensive, but the installation hours are much lower, so the installed costs are similar. The weight of the electric system with its batteries is less than that of the diesel engine with its fuel and exhaust systems, as well.
The footprint of the electric drive unit (note the orange supply lines) is impressively small. No fuel system and tank, no exhaust system. Also, no trips to the fuel dock, no smell, no emissions, and no noise. (There are a lot of batteries, of course!) Range is a constraint, just as it is with electric cars, but this will undoubtedly increase as battery technology continues to improve. Electric looks like the way of the future, both at sea and on the highway.
The keel went on early in this project, as raising the hull suited the multi-level layout of the Brooklin Boatyard shop. The leading edge strake and trailing edge fillet reduce interference drag around the keel root. The tapered laminate for the ‘box’ style bilge sump is evident, as is its opening in the hull.
The drawing showed a straight vertical inboard edge to the second bulkhead, but the crew thought it would look much better if it were cut away to match that of the main bulkhead. They drew their version with a marker, and they were right, of course. This is just one example of why it is so important (and so much fun!) to work with people that you know and respect, and that you trust to speak up when they have a better idea.
The bosses for the deck hardware are in place, and the bases for the lifeline stanchions are being fitted.
The next stop is the paint shop. Splashdown is getting closer every day.